導入事例
導入事例一覧
製造 | お客様名 | 従業員数 | 導入期間 |
---|---|---|---|
螺子 | 株式会社杉浦製作所様 | 550名 | 7ヶ月 |
ジャッキ、アルミダイキャスト | 川﨑工業株式会社様 | 400名 | 1年2ヶ月 |
鋳鉄、アルミダイキャスト | 中央可鍛工業株式会社様 | 580名 | 3年3ヶ月 |
トヨタ車体グループ様 |
中央可鍛工業株式会社様
導入背景
「業務の見直し・改善」と「基幹システム再構築」をセットで解決
弊社の基幹システムは、稼働後20年の間つぎはぎ的にシステム化を進めてきたため拡張性や自由度が無く、次第に時代変化に耐えられない状況となっていた。
特に問題なのが、ユーザ部門によって作成されるExcelのマクロやAccessなどの仕組みの蔓延により、情報システム部門が管理できないデータが氾濫するようになったことである。
その結果、データの一元管理ができなくなり経営状況の把握に時間と手間がかかるようになった。
また、業務プロセスが標準化されていないことによる非効率性、 および内部統制上の問題(データ管理上のリスクやデータの不整合)など様々な弊害が顕在化するようになった。
さらに、既存の基幹システムの技術文書(仕様書、設計書等)の不備も多く、プログラムの概要やデータ関連の調査が容易でない状況である。
現在の基幹システムの延長では『こうした課題を抜本的に解決することはできないであろう』との結論に至り、当プロジェクトは発足した。
コスト削減による増益体制へ変換
省人化 | 手作業の廃止による工数低減と精度向上 |
---|---|
見える化 | 必要な情報の一元管理を⾏い、有効活用できるシステム構築 |
業務標準化 | 事務業務の徹底的な標準化とそれを支えるシステム基盤整備 |
大部屋化 | 効率化、省人化できる組織作り |
スピードUP | リアルタイムでの情報把握 |
導入経緯
トヨタ系の生産管理システムに強いジャパン・テック・システムのノウハウを評価
基幹システム再構築、および、それに伴う業務改善支援を委託するベンダーを5社(大手2社・中堅3社)から選定する際に以下が決め手となった。
- トヨタ自動車の仕入先に対する経験値の高さ
- トヨタグループのEDIシステム「u-DIEX汎用」(TNS)との親和性の高さ
- トピックス社システム「トヨタ自動車の電子かんばん」「トヨタWG共通EDI」との親和性の高さ
- 課題に対する業務改善支援体制の厚さ
システム概要
iJITのオープン版に機能の追加・カスタマイズを行い新基幹システムを構築
主要システム一覧
- 生準システム
- 建仮システム
- Web調達システム(調達依頼~見積~発注~受入~受領~買掛)
- 生産システム(内示~所要量展開~かんばん枚数計算)
- 販売システム(内示~受注~出荷~検収~売掛~照合)
- 支給システム(支給依頼~出荷)
- 実績システム(生産実績~生産性評価~原価インターフェース)
- 年度計画システム
- デポ在庫システム
- 棚卸システム
導入成果
事務業務の標準化・システム化と、マスタの一元化・最新化を実現
ローカル管理されていたマスタ、品番・コード体系等を整理の上、部品表を核としたマスタの一元化を実現。
その結果、「部品表照会」にて製品の製造工程やその工程順が一目瞭然となった。
工程変更や単価変動などもいつでも変更履歴を照会可能になった。
残したローカルの仕組み(EUC)も基幹システムの演算結果を参照するように全面改修が出来た。
紙出力・郵送の手間を無くし、リアルタイムでの取引を実現
Webブラウザ専用システムにより協力会社・仕入先とインターネット経由の電子取引(WebEDI)を開始、紙出力・郵送の手間が削減された。
ITによる「内部統制」・「機密管理」のレベルアップ
個人認証/適切なユーザー権限の設定が可能となった。
利用ログが残り、不正や誤謬の追跡・再発防止も可能となった。
今後の展望
稼働率UP↑・不良率DOWN↓の「スマート工場」づくり支援
工場内の手書き業務の負荷や人為ミスを減らすためのIT推進。
独自規格で非互換であった工場内のFAシステムについて、近年登場したオープンな通信規格を基幹システムを軸に「つなぐ」ことに活用し、
工場内・外で発生している問題(ムダ・ムラ・ムリ) の「見える化」を図る。
お客様プロフィール
会社名 | ![]() |
---|---|
住所 | 愛知県日進市浅田平子1丁目300番地 |
資本金 | 10億3,600万円 |
売上高 | 209億円 |
従業員数 | 580名 |
事業内容 | 自動車部品・産業機械などの鋳鉄・アルミ鋳造製品 |
URL | https://www.chuokatan.co.jp/ |
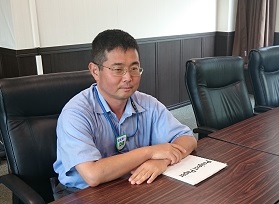
中央可鍛工業 係長様